Circularity in energy-efficiency retrofits: Why it’s time to act
The energy-efficiency retrofit market is poised to grow significantly, reaching $3.9 trillion by 2050. To maximize sustainability, circular economy principles—such as reusing materials, offering retrofit services, and increasing product transparency—are crucial. These practices can reduce waste, lower carbon emissions, and help materials manufacturers capture value in the expanding market. Stable regulation is key to unlocking the full potential of circular retrofitting.
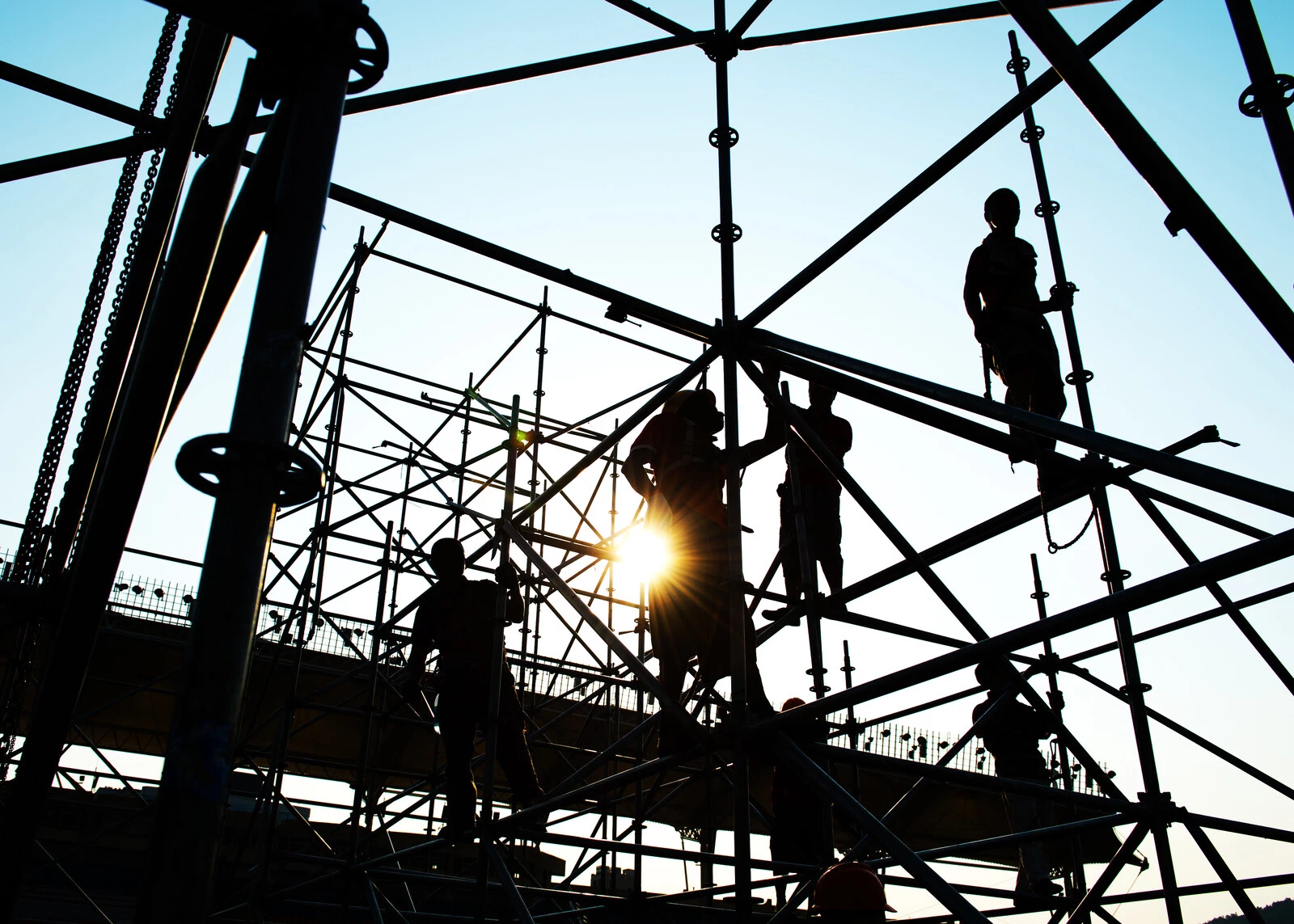
- The energy-efficiency retrofit market is expected to grow by 8% year over year from 2024 to 2050, from $500 billion to $3.9 trillion.
- The built environment ecosystem must recirculate materials and reduce virgin material extraction before this extensive wave of energy-efficiency retrofits.
- There are four circular ecosystem actions that materials and parts manufacturers can take to capture more value in this growing market.
The built environment consists of buildings and infrastructure that touch all aspects of human life—from our houses and apartments to the commercial and industrial spaces where we work, shop, and socialize. This ecosystem accounts for around 26% of global greenhouse gas (GHG) emissions.
Energy-efficiency retrofitting – also called upgrading or renovating – can reduce these GHG emissions and enhance climate resilience to mitigate the impact of extreme weather events on these structures. It involves upgrading existing assets to improve operational energy efficiency, extend useful life, reduce embodied carbon emissions and ensure regulatory compliance.
Retrofitting can also reduce the total cost of ownership and shorten construction times compared to new construction.
That said, energy-efficiency retrofitting may use virgin raw materials (resources extracted directly from nature without processing) and often presents a waste challenge because existing materials, which may still have a functional lifespan, are removed.
This is where circularity – optimizing resources and minimizing waste during production and consumption – can help by creating a closed-loop system.
What materials are required by the growing energy-efficiency retrofit market?
To achieve net zero, renovation rates must increase to approximately 3% to retrofit 20% of existing assets by 2030. This means that from 2023 to 2050, tens of billions of tonnes of materials will be required for energy-efficiency retrofits. These materials include plastic, mineral wool, glass, aluminium, flat steel and concrete, for example, according to the McKinsey analysis*.
Recent examples, such as the Entopia Building in Cambridge, UK, show the benefits of circular retrofit principles and the reuse of material on-site. Over 5,000 items were diverted from landfills during its construction, and approximately 3.8 tonnes of steel sections were reused, saving 2,000 kilograms of carbon dioxide equivalent. Overall, 84% of carbon was saved per square metre compared with a standard office fitout.
How can the energy-efficiency retrofit industry create a circular value chain?
The anticipated savings of energy-efficiency retrofitting cannot be realized unless the industry creates a circular value chain. There are seven key parts of the retrofit value chain that can capture value from the move to circularity:
Today, materials and parts manufacturers generate revenue by selling materials to upgraders and renovators, with the cost of goods driven by virgin raw material costs and substantial energy consumption. With the move to a circular ecosystem, four initial actions could help materials and parts manufacturers capture some of the value of the growing energy-efficiency retrofit market:
1. Increase product transparency
This includes providing lifecycle information such as Environmental Product Declarations and material passports. Manufacturers could also develop “green parts” with high levels of recycled material or create a dedicated “reuse” parts line to increase revenues.
Depending on the material, there could be an increased willingness to pay for green materials and parts with full lifecycle information that allows for end-to-end traceability. A recent McKinsey survey, which has not been published, shows that nearly 80% of decision-makers are willing to pay premiums for green glass, for example.
2. Create value-add retrofit services for existing customers
Incumbent manufacturers can provide retro-first services such as repairing and remedying existing materials to extend their useful life. For example, a cladding material manufacturer could replace a product that does not meet new standards or needs repair with an alternative that uses recirculated material.
3. Integrate horizontally across the retrofit value chain
Horizontal integration could increase a company's market share. It could include offering both upstream services, such as specification and procurement of circular materials for engineers, and downstream offerings, like specialist installation services. The McKinsey analysis* also shows that some organizations have seen a 10% to 20% uplift in revenue after incorporating a circular offering that includes circular business models and repair, care, and refurbishment services.
Providing specialized retrofit services can also address pain points in the market, such as a shortage of labour specializing in insulation installation for real estate.
4. Set up take-back mechanisms
Collaborations with other retrofit materials and parts manufacturers can help reduce virgin materials costs and secure circular feedstock material. Such arrangements often involve urban mining and reverse logistics, such as aluminium and glass organizations partnering to deconstruct and extract valuable materials from building façades.
This creates closed material loops. It reduces costs, environmental impact and reliance on virgin materials.
Circularity in energy-efficiency retrofitting is not just about financial value. Implementing these actions can also create environmental value via less reliance on virgin materials and lower energy costs. It creates social value, too, in the form of new jobs and reduces the impact of heavy industry on communities.
The key to all of this will be regulation and stability. Circularity in retrofitting represents a significant opportunity for the built environment, but industry players must be able to take action now to seize this opportunity.