Life cycle assessment of battery electric vehicles
Implications of future electricity mix and different battery end-of-life management
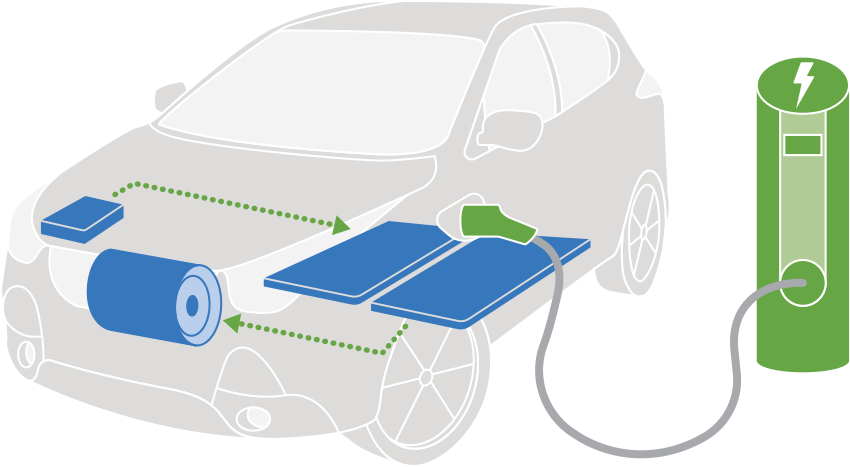
Abstract
The environmental performance of battery electric vehicles (BEVs) is influenced by their battery size and charging electricity source. Therefore, assessing their environmental performance should consider changes in the electricity sector and refurbishment of their batteries. This study conducts a scenario-based Life Cycle Assessment (LCA) of three different scenarios combining four key parameters: future changes in the charging electricity mix, battery efficiency fade, battery refurbishment, and recycling for their collective importance on the life-cycle environmental performance of a BEV. The system boundary covers all the life-cycle stages of the BEV and includes battery refurbishment, except for its second use stage. The refurbished battery was modelled considering refurbished components and a 50% cell conversation rate for the second life of 5 years. The results found a 9.4% reduction in climate impacts when future changes (i.e., increase in the share of renewable energy) in the charging electricity are considered. Recycling reduced the BEV climate impacts by approximately 8.3%, and a reduction smaller than 1% was observed for battery refurbishment. However, the battery efficiency fade increases the BEV energy consumption, which results in a 7.4 to 8.1% rise in use-stage climate impacts. Therefore, it is vital to include battery efficiency fade and changes to the electricity sector when estimating the use-stage impacts of BEVs; without this, LCA results could be unreliable. The sensitivity analysis showed the possibility of a higher reduction in the BEV climate impacts for longer second lifespans (>5 years) and higher cell conversation rates (>50%). BEV and battery production are the most critical stages for all the other impact categories assessed, specifically contributing more than 90% to mineral resource scarcity. However, recycling and battery refurbishment can reduce the burden of the different impact categories considered. Therefore, manufacturers should design BEV battery packs while considering recycling and refurbishment.
Highlights
-
The environmental impacts of electricity changes and battery end-of-life are assessed.
-
Changes in charging electricity reduced the climate change impact by 9.4%.
-
Vehicle production is the main driver of climate impacts in the dynamic scenario.
-
The impacts of refurbished batteries depend on reusable cells and the second use lifespan.
1. Introduction
The transport sector significantly contributes to the global environmental problems, including climate change (CC), air pollution and toxicity (Colvile et al., 2001; Hooftman et al., 2016; IPCC, 2018). Transport remains one of the most significant sources of greenhouse gas (GHG) emissions. In 2018, direct GHG emissions from transport accounted for approximately 24% of direct energy-related carbon dioxide (CO2) global emissions (IEA, 2020), with passenger road vehicles being the largest contributors accounting for 45% of global transport CO2 emissions (IEA, 2020). In contrast to all other sectors, the GHG emissions from the transport sector in the European Union (EU) increased by 0.9% and 0.8% in 2018 and 2019, respectively (EEA, 2020). Projections on existing mitigation measures estimate a 32% increase in transport emissions by 2030 compared to 1990 levels in the EU (EEA, 2020). Aggressive mitigation measures in the transportation sector are essential to reduce emissions in order to achieve the goals of the European Green Deal of reducing GHG emissions by 55% in 2030 and becoming climate-neutral by 2050 (European Commission, 2019).
Deploying battery electric vehicles (BEVs) is one of the main initiatives to decarbonise and reduce emissions from the transport sector, as they have no tailpipe emissions and can significantly reduce impacts on CC when charged with electricity from renewable energy sources (RESs) (Cox et al., 2018; Koroma et al., 2020). However, the environmental impact of their manufacturing is higher than that of internal combustion engine vehicles (Cox et al., 2018; Koroma et al., 2020) due to battery production, shifting the environmental burden from the use stage to production (Peters et al., 2017). The demand for larger battery sizes to tolerate longer driving ranges has exacerbated the problem. As a result, extending the life of used BEV lithium-ion batteries (LIB) for secondary application (hereafter referred to as ‘refurbished EV batteries’) has been proposed to reduce the environmental impact of battery manufacturing on the BEV life cycle (Casals et al., 2019; Hossain et al., 2019). Additionally, refurbishing EV batteries aligns with the EU's Circular Economy Action Plan to reduce or eliminate waste and pollution and transform products and materials to remain in supply chains for as long as possible (European Commission, 2020).
1.1. Environmental impacts of battery electric vehicles
Life cycle assessment (LCA) is a methodology standardised by ISO, 2006, ISO, 2006 to analyse the environmental impacts of products or systems. LCA has been widely applied to electric vehicles in the scientific literature (Hawkins et al., 2012; Marmiroli et al., 2018; Nordelöf et al., 2014; Peters et al., 2017). However, the existing studies found significantly different results due to their divergence in assumptions. However, most studies conclude that electricity production is the main driver of electric vehicles' climate impact, followed by battery production (Marmiroli et al., 2018; Peters et al., 2017). Furthermore, the importance of battery efficiency and refurbishment has been highlighted (Hossain et al., 2019; Peters et al., 2017). To that end, the following paragraphs examine how these aspects (electricity mix, battery efficiency and refurbishment) have been considered in LCA studies.
The CC impact of a BEV use phase depends on the carbon footprint of the electricity mix used to charge the vehicle (Marmiroli et al., 2018; Nordelöf et al., 2014). However, few studies have considered future changes in the charging electricity mix of BEVs (Cox et al., 2018, Cox et al., 2020; Koroma et al., 2020). Most LCA studies on BEVs have only used an average emission profile of the charging electricity mix for the first year of use throughout the vehicle's lifetime (Marmiroli et al., 2018). As the emission profile of the charging electricity mix will vary throughout the vehicle's lifetime due to expanding RESs (European Commission, 2019), there is a need for LCA studies of BEVs to include these changes throughout the vehicle's lifetime.
Peters et al. (2017) found that the efficiency of traction batteries is critical and can significantly impact the environmental performance of EV batteries and BEVs. Since the traction battery capacity and energy efficiency degrades over time and cycling (Birkl et al., 2017), Eftekhari (2017) and Redondo-Iglesias et al. (2019) found that the decrease in battery energy efficiency can directly influence the lifetime energy consumption of BEVs. Faria et al. (2014) also found that the capacity loss over time for the different BEV driving profiles (represented in terms of C-Rate) directly influenced the BEV energy consumption and the battery ageing mechanism. However, most LCA studies on BEVs have overlooked this aspect, as shown in review studies (Hawkins et al., 2012; Marmiroli et al., 2018; Nordelöf et al., 2014; Peters et al., 2017). In that context, there is a need to assess the environmental performance of a BEV considering the fade in battery capacity and energy efficiency.
From a life cycle perspective, extending the life of used BEV batteries in stationary applications is an initiative to improve the BEV and battery environmental performance (Hossain et al., 2019). After their first use in BEVs, traction batteries still have approximately 60% to 80% of their initial capacity, making them suitable for refurbishment and use in less-demanding applications (Casals et al., 2019). Several LCA studies have suggested environmental benefits when BEV batteries are refurbished (Ahmadi et al., 2017; Bobba et al., 2018; Faria et al., 2014; Richa et al., 2015; Schulz-Mönninghoff et al., 2021). However, different system boundaries are used in the scientific literature – Table 1. Most studies in Table 1, except for Ahmadi et al. (2014b), Casals et al. (2017), and Hill et al. (2020), delimited their system boundaries to the battery life cycle (covering its use in BEVs and secondary applications), excluding the vehicle equipment. The limitation of the system boundary to the battery life cycle does not support the understanding of the environmental performance of a BEV from a life cycle perspective (Schulz et al., 2020). This study aims to broaden the perspective on this issue in context.
Table 1
System boundaries of LCA studies on refurbished EV batteries. Legend: EoL – end-of-life, M – manufacturing, R – refurbishment, X – included, X* – only energy loss due to battery efficiency and the extra energy needed to carry the battery, X~ – only energy loss due to battery efficiency.
Author | Vehicle – M | Vehicle use | Vehicle EoL | Battery – M | Battery – R | Battery second use | Battery EoL |
---|---|---|---|---|---|---|---|
Cicconi et al. (2012) | X* | X | X | X | |||
Ahmadi et al. (2014b) | X | X | X | X | X | ||
Faria et al. (2014) | X | ||||||
Sathre et al. (2015) | X | ||||||
Ahmadi et al. (2017) | X | X | X | X | X | ||
Casals et al. (2017) | X | X | X | X | X | X | |
Richa et al. (2015) | X* | X | X | X | X | ||
Bobba et al. (2018) | X | X | X | X | |||
Cusenza et al. (2019b) | X | X | X | X | |||
Hill et al. (2020) | X | X | X | X | X | X | |
Koh et al. (2021) | X | X | X | X | |||
Schulz-Mönninghoff et al. (2021) | X~ | X | X | X | X |
1.2. Research motivation and novelty
As described, the environmental performance of BEV and refurbished EV batteries are widely studied but often separately, demonstrating a gap in the scientific literature. In addition, the combination of changes in the charging electricity mixes over time, battery efficiency fades, and refurbishment of EV batteries and recycling in the LCA of BEVs have not been investigated for their joint relevance on BEV environmental performance. This study presents an LCA study that integrates these aspects for the first time to assess the environmental performance of a present-day BEV. The following research questions are investigated:
-
1.What are the environmental impacts of a BEV charged with an average EU electricity mix in 2020?
-
2.How might these impacts change when the expected yearly increase in RES in the EU electricity mix is considered?
-
3.To what extent can refurbished EV batteries improve the net environmental performance of BEVs?
2. Materials and methods
A scenario-based LCA was performed based on the ISO 14040 and 14044 standards to assess the LC environmental impacts of a BEV (ISO, 2006, ISO, 2006). A complete vehicle LCA typically consists of two cycles: the equipment life cycle and the well-to-wheels (WTW) life cycle (Nordelöf et al., 2014). The equipment cycle covers all the processes involved in vehicle manufacturing, including material extraction and processing, component manufacturing, vehicle assembly, and end-of-life (EoL). The WTW cycle covers the energy carrier for vehicle propulsion, which is further divided into the well-to-tank (WTT) and tank-to-wheel (TTW) stages. The WTT stage includes all processes from the extraction of primary energy materials to energy conversion, distribution, and storage, while the TTW covers the vehicle operation stage.
The LCA was performed by considering changes in the charging electricity mix over time, battery efficiency fade, vehicle and LIB recycling, and LIB refurbishing. Fig. 1 shows the considered system boundaries and scenarios. The reference scenario included BEV production, the use stage (assuming an average EU electricity mix), and the EoL (vehicle and LIB recycling). In the dynamic scenario, the BEV use stage was assessed considering the projected changes in the EU electricity sector. The refurbished scenario considered the same projected changes in the EU electricity sector existing in the dynamic scenario and BEV refurbishment for a second use in a residential battery storage system.
The refurbished scenario assessed the BEV from its cradle to the grave, including its battery's refurbishment and EoL management. The second (stationary) use stage was excluded from the assessment for consistency with the functional unit and the aim of this study. Including the stationary use stage in the refurbished scenario will not reflect the BEV impact but that of the BEV plus stationary usage, which can add discrepancy to the results from the viewpoint of a BEV function. However, extending the life of the used BEV battery implies that the environmental burden of the LIB production and EoL stage could be shared between the BEV and the residential application. Therefore, the product substitution (avoided burden) approach was adopted to address the allocation issue (Majeau-Bettez et al., 2018). This approach extends the system boundary of the assessment to consider an equivalent new LIB (hereafter referred to as “avoided LIB”) in a stationary application by assuming that the refurbished LIB would displace the avoided LIB in practice. As a result, the environmental impacts avoided due to the production and EoL stages of the avoided LIB were then credited as avoided impacts to the BEV total environmental impacts.
The functional unit was defined as driving a European B-segment BEV equipped with a 54.6 kWh LIB for 160,000 km over a lifetime of 12 years (ACEA, 2019a). This functional unit was defined to match the characteristics and performance of Renault Zoe, an exemplary car of this segment (Renault, 2019). This vehicle segment is chosen as the small (A + B) cars representing 40% of total EU car sales from 2009 to 2020 (ACEA, 2021). Vehicle equipment production, battery pack assembly, use phase, and EoL were assumed to occur in Europe. The production of LIB cells was supposed to occur in South Korea. This assumption relies on the fact that a Korean company manufactures the LIB cells of Renault Zoe. In addition, over 88% of the current LIB cell manufacturing capacity is located in Asia (Lebedeva et al., 2016). The production of vehicle equipment and battery packs was assumed to occur in 2019. The BEV use stage was supposed to start in 2020 until its EoL in 2031, with no battery replacement considered. In the refurbished scenario, the LIB cells were refurbished at the EoL of the BEV for residential energy storage, extending its useful life for 5 years. This assumption stems from Casals et al. (2019) findings of 5.9 years for using refurbished EV batteries in buildings for self-consumption services at 60% EoL. However, Casals et al. found that the lifespan of refurbished EV batteries can range from approximately 4.7 to 30 years, depending on the second use. Therefore, a sensitivity analysis was performed on this parameter.
2.1. Life cycle inventory (LCI)
The LCI foreground data were compiled based on secondary sources, including the scientific literature, technical datasheets, reports, and brochures. Ecoinvent database v3.6 (Ecoinvent, 2019; Wernet et al., 2016) was used for the background data. The BEV modelled in this study was defined to characterise a medium-sized car similar to the Renault Zoe, equipped with a 54.6 kWh LIB (Renault, 2019). Further details on each life cycle stage are described in 2.1.1, 2.1.2, 2.1.3, 2.1.4, 2.1.5.
2.1.1. LIB and vehicle production
BEV production was considered for three main units: the vehicle glider, the electric axle drive (e-drive), and the battery system. The key characteristics of the considered BEV are shown in Table S1 of the Supplementary Material (SM) and its mass composition in Table 2. The LCI for glider production was adapted from the Ecoinvent dataset based on the “Golf A4” life cycle inventory from the 2000s (Schweimer and Levin, 2000; Wernet et al., 2016). Thus, the following changes were made to the original dataset from the Ecoinvent database to make the vehicle glider more representative of current passenger cars: the energy for glider assembly was modified to reflect the EU energy mix for the production year (2019), and the production of a 9.3-inch touchscreen tablet for in-vehicle infotainment system was added based on data from Teehan and Kandlikar (2013). The LCI for this change is reported in Table S2 of the SM.
Table 2
Mass composition of the battery electric vehicle components.
Unit | Components | Amount | Reference |
---|---|---|---|
Glider | Glider (kg) | 1150.1 | Authors' estimatea; Ecoinvent (2019) |
Electric axle drive | Gearbox (kg) | 23.8 | BRUSA (2019) |
Electric motor (kg) | 45.5 | Nordelöf et al. (2017); Nordelöf and Tillman (2017) | |
Inverter (kg) | 10.9 | Nordelöf et al. (2018); Nordelöf (2018) | |
Converter (kg) | 4.8 | BRUSA (2019); Ecoinvent (2019) | |
Charger (kg) | 12.0 | BRUSA (2019); Ecoinvent (2019) | |
PDU (kg) | 3.9 | BRUSA (2019); Ecoinvent (2019) | |
Li-ion battery system | Battery pack (kg) | 326.0 | NMC 111 cells based on Dai et al. (2018); Winjobi et al. (2020); battery pack components based on Ellingsen et al. (2014) |
The electric motor and inverter were modelled based on the scalable life cycle inventory model proposed in Nordelöf et al. (2017) and Nordelöf et al. (2018). The nominal power (100 kW) and the voltage (400 V) of the electric motor and inverter were used as input to the life cycle inventory model to estimate their respective mass and manufacturing data (see Table S3 and Table S4 for inventory data). The converter, power distribution unit, and onboard charger were based on BRUSA (2019), while LCI data and processes for these components were derived from the Ecoinvent database.
Table 3 shows the characteristics of the LIB cells in this study. The LIB cells contained a cathode based on nickel manganese cobalt (NMC) 111 and an anode with graphite as the active material. The NMC battery chemistry was chosen to match the battery pack of Renault Zoe better. In addition, in 2016, the NMC held approximately 26% market share in the overall LIB market (Pillot, 2017), with a projection to reach 63% by 2027 (Fitchsolutions, 2021). Overall, the modelled LIB cells make up 63% of the total mass of the battery pack (Renault, 2019). The production of the LIB cells was modelled based on Dai et al. (2018) and Winjobi et al. (2020). The manufacturing of battery pack components (battery packaging, cooling system, and battery management system) was based on Ellingsen et al. (2014). Finally, the battery pack components were rescaled based on their mass characteristics to represent the LIB capacity of the BEV. Detailed inventory data are provided in Table S5 of the SM.
Table 3
Characteristics of the LIB cells in this study (Winjobi et al., 2020).
Characteristics | NMC 111 |
---|---|
Cell nominal voltage (V) | 3.7 |
Nominal capacity (Ah) | 43 |
Battery cell efficiency (%) | 95 |
Cell energy density (Wh/kg) | 264.2 |
Battery pack energy (kWh) | 54.6 |
2.1.2. Vehicle use
The WTT stage of the BEV was modelled from 2020 to 2031 using the average annual mileage electricity consumption and the average electricity profile of each year. For the reference scenario, the average electricity mix for 2020 was used based on the “Stated Policies Scenario” for the EU (IEA, 2019), which assumes the continuity of the current policy measures. Projections for changes in EU electricity generation over time (Table S6 in SM) were used in the dynamic and refurbished scenarios.
The BEV energy consumption was calculated using the driving cycle defined by the Worldwide Harmonised Light Vehicle Test Procedure (WLTP) (ACEA, 2019b). The BEV mass, rolling resistance, and aerodynamic drag were used to calculate the mechanical energy at the wheels required to follow the WLTP cycle. For each time step set of the WLTP driving cycle, the motive force (Fm) and the power at the wheels (Pwheel) were estimated using Eqs. (1), (2), respectively. Additionally, the slope was set to zero through the driving cycle to simplify the calculation. The power supplied by the battery (EPsupply) was calculated using Eq. (3) considering the energy demand for auxiliaries (1740 W based on Miri et al. (2020) – see Table S7 for details) and the efficiency of all the drivetrain components. Additionally, the power from regenerative braking (EPrecover) was recovered using Eq. (4). The average energy supplied by the battery (Eavg) at the tank-to-wheel (TTW) stage was calculated with Eq. (5). Finally, the average energy consumption of the BEV (BEVenergy. cons) was calculated using Eq. (6) as 21.6 kWh/100 km, which considered the estimated yearly average fade in the BEV battery roundtrip efficiency.