Advances and perspectives in multi-material additive manufacturing of heterogenous metal-polymer components – Nature
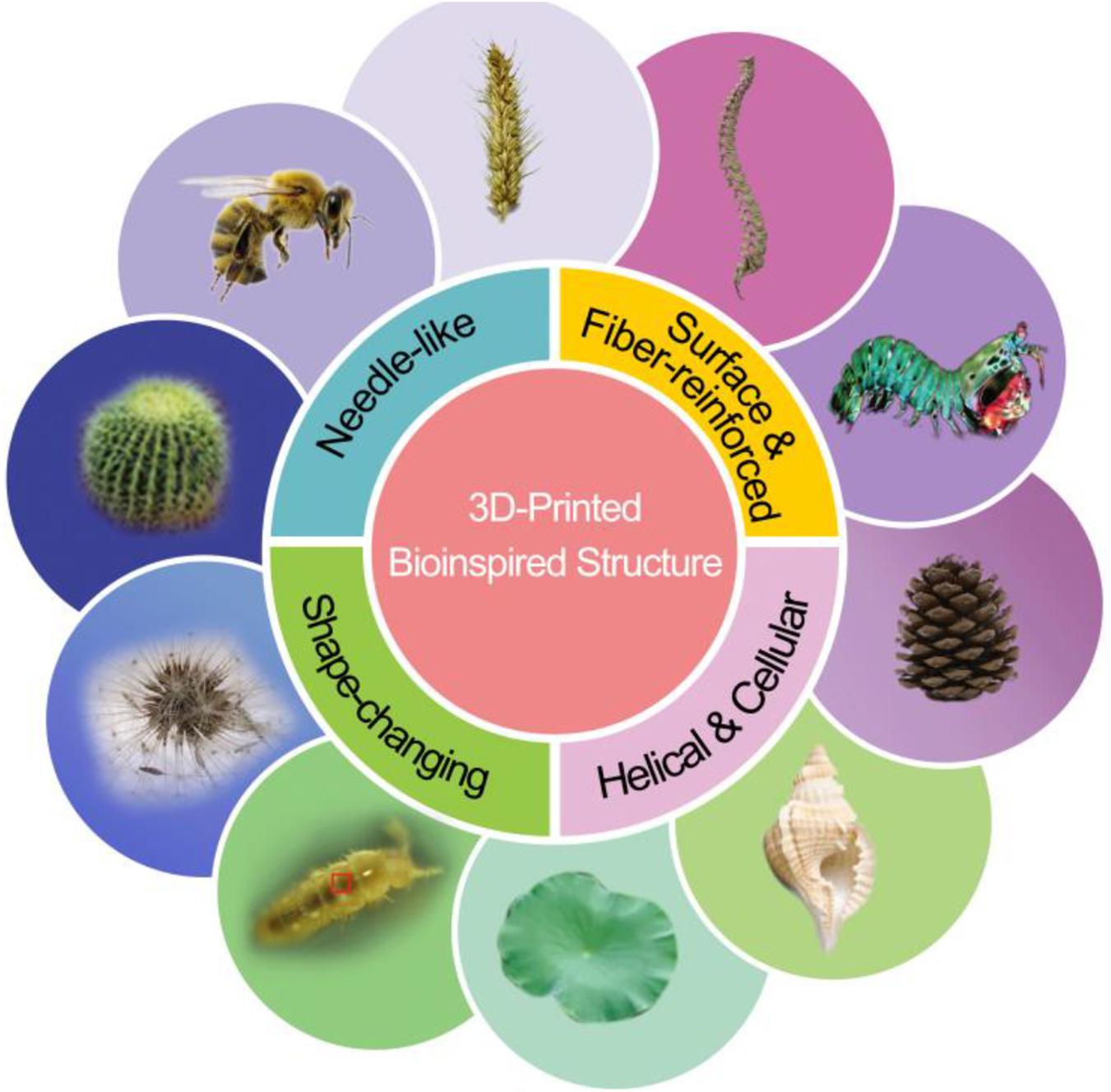
Executive Summary
This report provides a comprehensive analysis of recent advancements in multi-material additive manufacturing (MMAM), with a specific focus on the fabrication of heterogeneous metal-polymer components. These hybrid structures integrate the distinct properties of metals and polymers, offering significant potential for innovation across multiple industries. The fabrication methodologies are assessed through the lens of the United Nations Sustainable Development Goals (SDGs), particularly SDG 9 (Industry, Innovation, and Infrastructure), SDG 12 (Responsible Consumption and Production), and SDG 7 (Affordable and Clean Energy). The report categorizes fabrication techniques into direct printing and hybrid manufacturing, evaluating their scalability, material compatibility, and functional performance. It concludes by identifying critical challenges and outlining future research directions toward developing scalable, high-performance, and sustainable metal-polymer systems that contribute to global sustainability targets.
1. Introduction: MMAM as a Driver for Sustainable Industrialization
The global manufacturing landscape is shifting towards processes that are more efficient, adaptable, and sustainable. Multi-material additive manufacturing (MMAM) is at the forefront of this transformation, enabling the fabrication of complex, multifunctional structures that were previously unachievable. By integrating dissimilar materials, MMAM directly supports the objectives of SDG 9: Industry, Innovation, and Infrastructure, by upgrading industrial capabilities and fostering innovation.
Among the various material combinations, metal-polymer hybrids are particularly promising. They combine the mechanical strength and conductivity of metals with the lightweight and flexible properties of polymers. This synergy allows for the creation of optimized components that enhance resource and energy efficiency, a key target of SDG 12: Responsible Consumption and Production and SDG 7: Affordable and Clean Energy. Applications for these advanced materials are emerging in critical sectors:
- Aerospace and Automotive: Lightweighting of components to reduce fuel consumption and emissions.
- Electronics: Miniaturized and integrated circuits for more efficient devices.
- Biomedical: Customized implants and devices, contributing to SDG 3: Good Health and Well-being.
However, the integration of these disparate materials presents significant challenges, including interfacial adhesion and thermal incompatibility. This report reviews current manufacturing strategies designed to overcome these hurdles, assessing their potential to drive sustainable industrial progress.
2. Fabrication Strategies for Metal-Polymer Hybrids
The fabrication of metal-polymer components can be broadly classified into two categories: direct printing processes and hybrid manufacturing methods. Each approach offers unique advantages and challenges in the context of creating sustainable and functional products.
2.1. Direct Printing of Metal-Polymer Hybrids
Direct printing methods aim to fabricate metal-polymer structures in a single, integrated process, which can enhance production efficiency and reduce waste, aligning with the principles of SDG 12. These techniques represent significant technological innovations supporting SDG 9.
- Electrical Field-assisted Heterogeneous Material Printing (EF-HMP): This single-step, room-temperature process allows for the precise deposition of metallic particles onto a polymer matrix. By avoiding high temperatures, it reduces energy consumption and enables the use of thermally sensitive polymers, contributing to both SDG 7 and SDG 12.
- Polymer-assisted Photochemical Deposition (PPD): PPD utilizes light to initiate a chemical reaction that deposits metallic films on polymer substrates. This technique eliminates the need for energy-intensive vacuum processes and complex lithography, offering a more sustainable pathway (SDG 12) for producing high-resolution optical and electronic devices.
- 3D Polymerization-Induced Phase Separation (3D PIPS): This method creates functionally graded materials by controlling the phase separation of materials during photopolymerization. It improves the structural integrity of metal-polymer interfaces, leading to more durable and long-lasting products, which reduces the need for replacements and conserves resources (SDG 12).
2.2. Hybrid Manufacturing of Metal-Polymer Hybrids
Hybrid methods combine AM with traditional post-processing techniques to achieve metallization. While highly effective, these processes present challenges related to environmental impact, highlighting the need for responsible innovation under SDG 9 and SDG 12.
2.2.1. 3D Printing Combined with Electroplating and Electroless Plating
This common hybrid approach uses 3D printing to create a polymer scaffold, which is then coated with metal through plating.
- Benefits: This method produces robust, conductive surfaces on complex geometries, enabling the creation of advanced electronics, antennas, and sensors. The ability to create lightweight yet strong structures supports energy efficiency goals (SDG 7).
- Sustainability Challenges: Both electroplating and electroless plating processes often involve hazardous chemicals and produce toxic waste. This presents a direct conflict with SDG 12.4, which calls for the environmentally sound management of chemicals and wastes. Future innovation must focus on developing greener, non-toxic plating solutions and closed-loop recycling systems to make this a truly sustainable manufacturing route.
2.2.2. Alternative Joining and Reinforcement Techniques
To address adhesion issues and improve structural performance, several alternative methods are being explored. These techniques enhance product durability and longevity, supporting the resource efficiency goals of SDG 12.
- Mechanical Interlocking and AddJoining: These methods create strong bonds by physically interlocking the metal and polymer components during the AM process, avoiding the need for adhesives or chemical treatments.
- Thermomechanical Joining: This process uses heat and pressure to fuse materials, creating strong, reliable joints for load-bearing applications.
- Compression Overmolding: This technique combines AM-produced metal lattices with overmolded polymer composites, resulting in exceptionally stiff and strong hybrid structures suitable for lightweighting applications in the automotive sector, thereby contributing to SDG 7.
3. Sustainable Development Impact and Applications
The development of metal-polymer hybrid MMAM has a direct and significant impact on several SDGs by enabling the production of more efficient, durable, and functional products.
3.1. Contribution to SDG 9: Industry, Innovation, and Infrastructure
MMAM is a cornerstone of Industry 4.0, fostering innovation and upgrading technological capabilities. By enabling the creation of integrated, multifunctional components (e.g., structures with embedded sensors and circuits), these technologies are building more resilient and advanced industrial infrastructure.
3.2. Contribution to SDG 12: Responsible Consumption and Production
MMAM contributes to sustainable production patterns in several ways:
- Waste Reduction: As an additive process, 3D printing generates significantly less material waste compared to traditional subtractive manufacturing.
- Resource Efficiency: The creation of lightweight components for transportation reduces fuel consumption over the product’s lifecycle.
- Product Longevity: Enhanced interfacial strength and durability lead to longer-lasting products, reducing waste and the demand for raw materials.
- Chemical Management: A critical area for improvement is the development of sustainable alternatives to hazardous plating chemicals, which is essential for achieving environmentally sound production.
3.3. Contribution to SDG 7: Affordable and Clean Energy
The technology supports clean energy goals by:
- Improving Energy Efficiency: Lightweighting in aerospace and automotive sectors directly reduces energy consumption. More efficient electronic components also lower power demand.
- Enhancing Energy Storage: Innovations in hybrid materials, such as metal-organic frameworks (MOFs) in polymer electrolytes, are leading to safer and higher-performance batteries.
4. Future Outlook: Towards a Sustainable MMAM Ecosystem
The full potential of metal-polymer MMAM can only be realized by addressing its current limitations through a lens of sustainability. The future of the field depends on progress in several key areas:
- Development of Green Materials and Processes: A primary focus must be on creating recyclable polymers and environmentally benign metallization techniques to replace toxic plating processes. This is crucial for aligning with SDG 12.
- Data-Driven Process Optimization: The use of machine learning and digital twins can optimize manufacturing parameters to minimize material waste, reduce energy consumption, and predict component performance, further advancing the goals of SDG 9 and SDG 12.
- Enhancing Interfacial Compatibility: Continued research into surface functionalization, novel compatibilizers, and nanoscale fillers is needed to ensure the long-term durability and reliability of hybrid components.
- Scalability and Standardization: Establishing industry-wide standards for testing and certification will be essential for the widespread adoption of these technologies in critical applications, ensuring they contribute effectively to a sustainable industrial economy.
In conclusion, metal-polymer hybrid MMAM is a transformative technology poised to redefine manufacturing paradigms. By prioritizing sustainable innovation, interdisciplinary collaboration, and responsible design, this field can deliver smarter, lighter, and more sustainable solutions that are integral to achieving the Sustainable Development Goals.
Analysis of Sustainable Development Goals in the Article
1. Which SDGs are addressed or connected to the issues highlighted in the article?
The article on multi-material additive manufacturing (MMAM) of metal-polymer hybrids connects to several Sustainable Development Goals (SDGs) by focusing on technological innovation, industrial advancement, sustainable practices, and applications in key sectors like energy and health.
-
SDG 9: Industry, Innovation, and Infrastructure
This is the most prominent SDG in the article. The entire text is a review of “recent innovations” in manufacturing technologies (MMAM). It discusses upgrading industrial capabilities by developing “cost-effectiveness,” “shorter lead times,” and “greater material adaptability.” The goal is to build resilient infrastructure and foster innovation by creating “scalable, high-performance, and sustainable metal-polymer hybrid systems.” The article highlights how these technologies are “driving innovations across industries, including aerospace, automotive, electronics, and biomedical applications.”
-
SDG 12: Responsible Consumption and Production
The article addresses the need for more sustainable manufacturing patterns. It explicitly mentions considering “potential environmental impacts” of metallization techniques. There is a call to develop “environmentally friendly electroplating processes” and “environmentally sustainable alternatives” to replace methods that use “toxic chemicals.” This aligns with the goal of achieving environmentally sound management of chemicals and reducing waste. The development of “recyclable materials” is also noted as a key area for future research.
-
SDG 7: Affordable and Clean Energy
The article connects to this goal through its discussion of applications in energy storage. It describes the fabrication of “electrochemical energy storage devices” and improving “lithium-ion batteries” by using metal-polymer hybrids to “suppress dendrite growth.” Furthermore, by creating more efficient electronic components with lower resistance, such as solenoids where resistance was reduced “from 3 kΩ to 18.7 mΩ,” these technologies contribute to overall energy efficiency.
-
SDG 3: Good Health and Well-being
The article repeatedly points to the use of MMAM in “biomedical applications.” Specific examples include producing a “customized dental implant” and “implantable high-gain dental antennas for minimally invasive biomedical devices.” The development of materials with “antibacterial inhibition zones” also contributes directly to health and well-being by creating safer medical devices.
2. What specific targets under those SDGs can be identified based on the article’s content?
Based on the issues discussed, several specific SDG targets can be identified:
-
Under SDG 9 (Industry, Innovation, and Infrastructure):
- Target 9.4: “By 2030, upgrade infrastructure and retrofit industries to make them sustainable, with increased resource-use efficiency and greater adoption of clean and environmentally sound technologies and industrial processes…” The article directly supports this by reviewing advanced manufacturing processes (MMAM) that are more efficient and exploring “environmentally friendly metallization processes.” The focus on “process efficiency” and “cost factors” aligns with retrofitting industries for sustainability.
- Target 9.5: “Enhance scientific research, upgrade the technological capabilities of industrial sectors in all countries…encouraging innovation…” The article is a comprehensive review of “recent advancements in MMAM” and concludes by “outlining future research directions.” This directly contributes to enhancing scientific research and upgrading technological capabilities in high-tech industrial sectors.
-
Under SDG 12 (Responsible Consumption and Production):
- Target 12.2: “By 2030, achieve the sustainable management and efficient use of natural resources.” Additive manufacturing, the core technology discussed, is inherently more resource-efficient than traditional subtractive methods. The article also emphasizes “material compatibility” and “process efficiency,” which are key to the efficient use of resources.
- Target 12.4: “By 2020, achieve the environmentally sound management of chemicals and all wastes…” The article highlights the negative environmental impact of conventional plating, which involves “toxic chemicals,” and calls for “environmentally sustainable alternatives” and “eco-friendly printing and electroplating materials.”
-
Under SDG 7 (Affordable and Clean Energy):
- Target 7.a: “By 2030, enhance international cooperation to facilitate access to clean energy research and technology…and promote investment in energy infrastructure and clean energy technology.” The research presented on improving “electrochemical energy storage devices” and creating “high-efficiency electronic components” is a direct contribution to advancing clean energy technology.
-
Under SDG 3 (Good Health and Well-being):
- Target 3.d: “Strengthen the capacity of all countries…for early warning, risk reduction and management of national and global health risks.” The development of advanced “biomedical applications,” such as customized implants and minimally invasive devices, strengthens the technological capacity of the healthcare sector to manage health risks.
3. Are there any indicators mentioned or implied in the article that can be used to measure progress towards the identified targets?
The article mentions or implies several quantitative and qualitative indicators that can measure progress towards the identified targets.
-
For SDG 9 Targets:
- Process Scalability: Mentioned as a key challenge and goal, indicating progress in industrial adoption.
- Functional Performance Metrics: The article provides specific values for electrical conductivity (resistivity as low as “1.9 × 10−8 Ω⋅m”), mechanical strength (“ultimate lap-shear strength of 21.9 ± 1.1 MPa”), and thermal stability. These are direct measures of technological capability (Target 9.5).
- Cost-Effectiveness and Lead Times: The introduction identifies “cost-effectiveness” and “shorter lead times” as essential characteristics, which can be measured to track industrial efficiency (Target 9.4).
-
For SDG 12 Targets:
- Use of Toxic Chemicals: The reduction or elimination of “toxic chemicals” in processes like electroplating is a clear indicator for environmentally sound management of chemicals (Target 12.4).
- Development of Recyclable Materials: The call for “recyclable materials” is an implied indicator for reducing waste and promoting a circular economy (Target 12.5).
- Process Efficiency: Mentioned as a key consideration, which relates to the efficient use of natural resources (Target 12.2).
-
For SDG 7 Targets:
- Energy Density and Capacity Retention: The article mentions a “221% increase in volumetric energy density and superior capacity retention” for new energy storage designs, serving as direct indicators for improved clean energy technology (Target 7.a).
- Electrical Resistance: The reduction of resistance in electronic components (e.g., from “3 kΩ to 18.7 mΩ”) is a quantifiable measure of improved energy efficiency (Target 7.a).
-
For SDG 3 Targets:
- Biocompatibility and Antibacterial Properties: The ability to create surfaces with “bacterial inhibition zones” is a measurable indicator of improved health outcomes from medical devices (Target 3.d).
- Feasibility of Customization: The successful fabrication of a “customized dental implant” indicates progress in personalized medicine and healthcare technology (Target 3.d).
4. Table of SDGs, Targets, and Indicators
SDGs | Targets | Indicators (Mentioned or Implied in the Article) |
---|---|---|
SDG 9: Industry, Innovation, and Infrastructure |
9.4: Upgrade infrastructure and retrofit industries to make them sustainable.
9.5: Enhance scientific research and upgrade technological capabilities. |
|
SDG 12: Responsible Consumption and Production |
12.2: Achieve sustainable management and efficient use of natural resources.
12.4: Achieve environmentally sound management of chemicals and wastes. |
|
SDG 7: Affordable and Clean Energy | 7.a: Enhance access to clean energy research and technology. |
|
SDG 3: Good Health and Well-being | 3.d: Strengthen capacity for management of health risks. |
|
Source: nature.com